Rockbuild's Specialized Focus on Remedial Services
At Rockbuild, we have a specialized focus on the remedial sector of our industry. Our core expertise lies in providing a wide range of remedial services to our civil and commercial clients. These services include but are not limited to concrete repairs, concrete crack injection, and grouting. We take pride in our team of highly trained and experienced technicians who are equipped with the knowledge and skills required to deliver exceptional remedial services to our clients. At Rockbuild, we strive to offer personalized solutions that cater to the unique needs of each client, ensuring that their concrete structures are restored to their optimal condition.
Our Remedial Services
Concrete crack injection
The concrete crack injection can be used in a variety of ways to repair structural cracks or for waterproofing purposes. Rock Build can provide a tailored solution to your concrete crack requirements for a cost-effective price.
Concrete repairs
Concrete repair is widely provided when concrete cancer or spalling has occurred on existing structures. Our team of engineers at Rock Build can determine the extent of the repair required and provide a structurally sound solution for the project at hand.
Grouting
Rock Build Services offers a comprehensive range of grouting to the civil infrastructure, mining & building industries. Our team have a wealth of experience and a proven track record for all grouting and pressure grouting.
Water Blasting
Water blasting is a form of abrasive blasting used in multiple industries for different purposes. Rock Build with our specialised equipment can provide water blasting services to suit your project requirements.
SAND BLASTIng
Sandblasting is a form of abrasive blasting primarily used for removing existing coatings and contaminants. Rock Build with specialised sand blasting equipment can provide services to all tasks at hand.
Understanding
Remedial Maintenance Construction
Remedial maintenance construction is a vital process that involves repairing or improving existing structures and systems to ensure their functionality, safety, and aesthetic appeal. This type of construction can encompass a wide range of projects, ranging from minor repairs to major renovations or upgrades.
The importance of remedial maintenance construction cannot be overstated. Neglecting maintenance can lead to costly repairs and even compromise the safety of the building's occupants. It is therefore essential to regularly maintain structures and systems to prevent small issues from developing into major problems that could be expensive to fix.
There are various types of remedial maintenance construction projects, including repairing leaky roofs, replacing faulty electrical wiring, fixing plumbing issues, repainting walls, and upgrading heating and cooling systems. These projects require specialized skills and knowledge to complete effectively and efficiently.
To ensure the success of remedial maintenance construction projects, construction companies must adhere to best practices. This includes conducting a thorough inspection of the building to identify all issues that require attention, creating a detailed plan and timeline for the work, and using high-quality materials and equipment. Additionally, it is important to communicate effectively with clients to manage expectations and ensure they are satisfied with the final result.
In conclusion, remedial maintenance construction is a crucial process that helps to maintain the functionality, safety, and aesthetic appeal of existing structures and systems. With proper planning, communication, and execution, construction companies can successfully complete these projects and ensure the longevity of the buildings they work on.
"Making an investment in remedial maintenance construction today can prevent the need for expensive repairs in the future."
Why Is Remedial
Maintenance Construction Important?
It is essential for construction companies to recognize the significance of remedial maintenance construction, which involves repairing or enhancing existing structures and systems to restore their functionality, safety, and aesthetic appeal. This type of construction encompasses a broad spectrum of projects, from minor repairs to major renovations or upgrades.
The following are the reasons why remedial maintenance construction is crucial for construction companies:
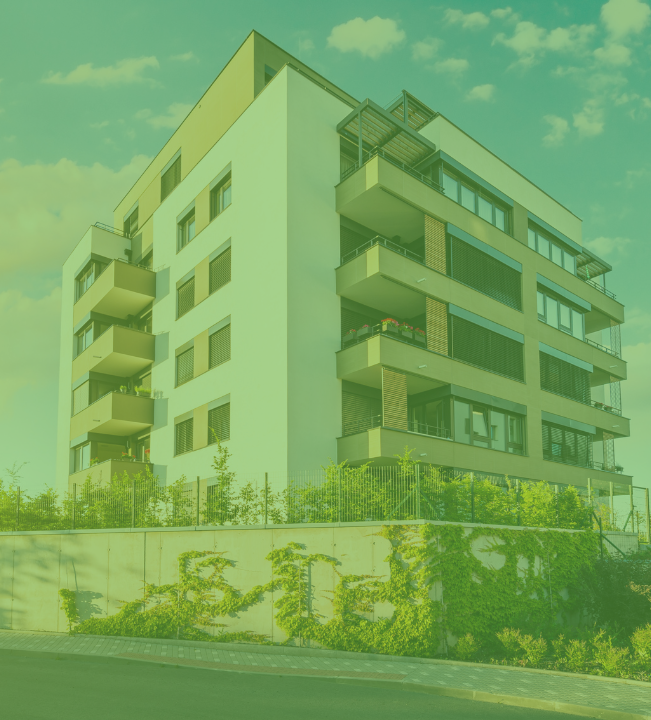
01
Cost Saving and Safety
Remedial maintenance construction is crucial for construction companies as it can help save costs in the long run and ensure the safety of building occupants and visitors. By maintaining or enhancing existing structures and systems, construction companies can avoid the need for costly repairs or replacements in the future, while prolonging the lifespan of buildings and equipment, reducing waste, and minimizing the frequency of replacements.
02
Regulation
compliance
Buildings and infrastructure systems are often required to meet various regulations at the local, state, and federal levels, such as building codes, safety standards, and environmental requirements. To comply with these regulations, your company can undertake remedial maintenance construction projects to ensure that your structures and systems meet the necessary standards. By doing so, your company can avoid potential penalties or legal problems and demonstrate ethical and responsible operation.
03
Aesthetics
The visual appeal of buildings and infrastructure systems can greatly affect their worth and usefulness. Undertaking remedial maintenance construction projects can assist your company in enhancing the aesthetics of these structures and systems, resulting in increased appeal and functionality for occupants and visitors. This can lead to improved property values and heightened attraction for potential business or tenants.
04
Sustainability
Remedial maintenance construction has the potential to advance sustainability goals by decreasing waste and energy usage. Upgrading mechanical and electrical systems, for instance, can enhance energy efficiency and lower maintenance expenses in the long run. Additionally, opting for high-quality materials and creating durable designs can assist in diminishing the environmental impact of construction projects.
Types of Remedial Maintenance Construction Projects
There exist numerous categories of projects that fall within the scope of remedial maintenance construction. Some of the typical examples are:
- Structural repairs: These projects involve repairing or strengthening the structural components of buildings or infrastructure systems. This might entail fixing wall cracks, repairing damaged beams or columns, or reinforcing foundations.
- Mechanical and electrical upgrades: Upgrading mechanical and electrical systems can boost energy efficiency and reduce maintenance expenses over time. This may include replacing outdated HVAC systems, upgrading lighting fixtures, or installing new plumbing.
- Waterproofing and roofing repairs: Water damage can cause severe issues in buildings and infrastructure systems. Remedial maintenance construction can involve fixing roofing leaks, setting up new waterproofing membranes, or reinforcing walls to prevent water infiltration.
- Facade repairs: The exterior of a building is critical for both aesthetic and structural reasons. Facade repairs encompass fixing cracks or damage to exterior walls, replacing doors or windows, or installing new cladding.
Best Practices for Remedial Maintenance Construction
In order to achieve effective remedial maintenance construction projects, construction companies should adhere to best practices, including:
Conducting thorough assessments
Conducting a comprehensive evaluation of the existing structure or system prior to commencing any remedial maintenance construction project is crucial. This can assist in identifying any underlying issues that need to be resolved and guarantee that the project addresses the root cause of the problem.
Using high-quality materials:
Using high-quality materials can help ensure that repairs or upgrades last for an extended period. This may include utilizing durable building materials, energy-efficient systems, and high-quality finishes.
Hiring experienced contractors:
Remedial maintenance construction projects can be complex and require specialized knowledge and experience. Engaging experienced contractors can help ensure that the project is completed on time, within budget, and up to the highest quality standards.
Staying up to date on regulations:
Construction companies should stay informed of local, state, and federal regulations related to building codes, safety requirements, and environmental standards. This can assist in ensuring that the project is compliant and avoids any potential legal issues.
Remedial maintenance construction is a vital aspect of maintaining and enhancing the safety, longevity, and functionality of existing structures and systems. These projects are essential in addressing underlying problems, reinforcing structures, and upgrading systems to meet current standards and regulations.
To achieve successful remedial maintenance construction projects, construction companies should adhere to best practices, including conducting thorough assessments before commencing any work. By doing so, companies can identify underlying issues that need to be addressed and ensure that the project targets the root cause of the problem.
Using high-quality materials is also critical in ensuring that repairs or upgrades last for an extended period. High-quality materials, including durable building materials, energy-efficient systems, and high-quality finishes, can help improve the lifespan of the structure or system while reducing maintenance costs over time.
Furthermore, hiring experienced contractors is crucial in remedial maintenance construction projects, which often require specialized knowledge and experience. Engaging experienced contractors can help ensure that the project is completed within budget, on time, and up to the highest quality standards.
Staying up to date on local, state, and federal regulations related to building codes, safety requirements, and environmental standards is also important. It can help construction companies ensure that the project is compliant and avoids potential legal issues.
In summary, remedial maintenance construction is an essential aspect of maintaining and enhancing existing structures and systems. Following best practices and utilizing high-quality materials and experienced contractors can help construction companies ensure that these projects are completed successfully and contribute to the safety and longevity of the built environment.